Often, in companies, Operations and Research & Development (R&D) are at odds. This is relatively natural. Operations typically spends their time working toward maximizing efficiency by making things as predictable and consistent as possible to save time and money. In the meantime, R&D is constantly working on ways to create new and different ways to operate. Development of disruptive change is rarely efficient and even more rarely low cost. Thus, Operations often just wants R&D to stop running tests and suggesting change and let them do what they are best at, while R&D is constantly asking “what if” questions that (when answered correctly) have the chance to deliver dramatic solutions and completely alter current reality. Over the course of our history, our little organization has had a profound impact on the industries in which we work because our global teams have been willing to work through these very challenging realities and deliver amazing solutions in both Operations and R&D to our customers.
We are in the midst of an amazing time right now folks, despite a grim Spring! After a strong year in 2014, we are simultaneously investing in improving our barns & field facilities to fight AI and also continue to fund our future in the form of promising R&D efforts. In the meantime, our tech team has been pulled in both directions to provide support and guidance. These combined efforts are paying off in both areas!
In May we released a now-declassified teaser picture to hint at what our LSI R&D engineering team has been working on (click HERE to reread that post). Today, we’re excited to bring the organization up to speed on an innovation project that is at least 40 years in the making. Over the past few months, our team has started the submission process with the U.S. patent office and are awaiting official notice that we have been granted Intellectual Property (IP) rights for a handful of patented pieces of our new nursery brooding process, so we can finally disclose more about what we are engaged in developing.
Our LSI R&D team, led by Shawn Engstrom, has been working on improving our turkey brooding performance for the last 2.5 years. The problem has always been that first egg poults are weak and frail compared to those from eggs laid later in a cycle. Currently, these poults take a lot more care to raise, to avoid a high mortality rate. As a result, they can be a liability to our customers when they receive them. The first week of a first-egg poult’s life is particularly risky. The potential solution that we have been seeking for years, is the development of a specialized brooding facility that would help ensure the survivability of these poults for that first week, and remove the risk for the individual grower. There would be huge value to the industry if someone could provide such a service.
For the past 40 years efforts to solve this problem have been elusive due to high costs, excessive labor, waste management, feed & water delivery issues, lighting, temperature and ventilation problems. With robotics costs coming down, LED light technology maturing and other technological advancements coming into the mainstream, we launched a project a few years ago to again look at answering this industry challenge. Early on, Nova-Tech Engineering was instrumental in moving this project forward by allowing access to their rapid prototyping equipment. Shawn and his resident senior engineer, Paul Wreede, were able to quickly design, print and test prototypes and bring concepts to life in days rather than months. This dramatically reduced the time to market for this product. With each failure we knew a little more, and lots of lessons learned have led to a handful of breakthroughs that could potentially change the turkey industry.
A custom-designed basket has accomplished what no one else has been able to discover: a way to manage the waste of growing turkeys that also allows for free movement of the birds. The holes in the floor of these baskets must be manufactured to extremely tight tolerances to come out a perfect size and shape that works for the birds. After many iterations, our R&D team’s injection-molded prototype baskets allow the perfect introductory environment for our new-born poults to grow and thrive. We have made a massive investment in the creation of these baskets and have partnered with a die-maker in China to produce a mold to make as many replica baskets as we’ll need. You can view the video below for a quick look at the process that goes into making an individual basket from this massive steel mold. Test baskets arrived in May and were tweaked to our satisfaction, and now the 24 ton die is halfway across the Pacific ocean on its way to our manufacturing partner in Iowa.
This innovation allows us to take on relatively low-risk responsibility of a new long-term goal: Providing all of our customers healthy, 10-day-old poults. Success means that we will finally succeed at taking out the early risks that are inherent in potentially fragile poults. Creating facilities that can deliver superior, low-risk birds to our customers will allow us to charge more per bird while providing them with an ideal environment in which they can thrive. This is a holy-grail discovery that has been hard-won, and we are proud to again lead the industry world-wide in releasing a service that has been pursued for four decades.
Now comes the most important part of any new discovery; effective collaboration with our Operations team to integrate this new opportunity into the amazingly efficient system we so expertly manage from day-to-day. This will not be easy, but our group is up to the challenge! Every member of our Ag Sector will be a part of figuring out how to make the most out of this new innovation, and success will be highly reliant on exceptional teamwork between groups that at times are naturally at odds. Despite the difficulty of change, our teams have historically proven to be willing to tackle those challenges and achieve success. As we move forward, the next phase in this project will require successfully partnering with Willmar Logistics, FSE, WPF, our hatcheries all over the country and the Agforte technical team to transition this new facility into another piece of our proven operational success.
Industrial Park Hatchery Thank you!
I (Mike Bregel) was recently at the AgForte Industrial Park Hatchery working with Dr. Dave Mills and North Division Hatchery Manager Neil Miller on a Bio Security video. I would like to give a big shout-out and thank you to Josh Liestman (Production Supervisor) for stepping up to the plate to be our actor. Most people scatter (can’t blame you!) when I come around with a camera and Josh willingly stepped in front of the lens. He endured the repetitive opening of doors and washing of hands as I tried to get every angle possible.
The Industrial Park Hatchery (IPH) in Willmar has the largest output of Poults worldwide and in spite of the recent AI outbreaks are only down 20% in production from max capacity. All of our agricultural facilities are currently working to minimize AI risk for this fall. The IPH has boosted biosecurity by including adding floor pans, requiring extra PPE for employees as well as visitors, re-education of employees on biosecurity procedures, the installation of foamers on doorways in between clean and dirty areas, and visitors are now screened at the doors before being allowed into the building(s).
Employee Announcements
Our long term collaborator, Dr Mohamed E. El Halawani at the University of Minnesota is retiring, and we’re sad to see him go. We recently stumbled on some old field research pictures from 20+ years ago (thanks Graham). Pictured here in their stylish WPF outfits are (from left to right): Graham Cox, Randy Skare, Mohamed Halawani and Darren Straub.
HR/Employee Services
The Human Resources/Employee Services Team specializes in benefits and payroll, compliance and policy, employee relations, ag-recruiting, legal compliance, and company & employee overall well-being. We are located on the first floor of Life-Science Innovations on the MinnWest campus at 1800 Technology Drive. We look forward to working with you!
Please message us via email at employee.services@life-scienceinnovations.com or give us a call at
320.222.9515 or 888.320.9750 extension 2515
Recruiting Corner
Hello from Michelle Falling, MN Affiliates Recruiting Specialist
I hope everyone enjoyed the holiday weekend and feeling back ‘in a groove’! Recently we’ve had a couple of internal transitions happen which has been a fun process! Our culture of allowing employees to transition into roles that play to strengths came into play in both situations.
As always, message me with any questions you have regarding the new opportunities posted or if you want to talk through your career goals here at michelle.falling@life-scienceinnovations.com | or just give me a call at O: (320) 222-9790 M: (320) 441-8596. Thanks for trusting me to help you through the process!
Openings
Current status of all organizational openings.
Welcome New Employees

Christopher Krueger
Account Management
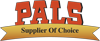
Carter Christopher
Service Technician
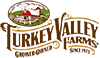
Halima Aden Ahmed
Miguel Ruiz Colon
Jose Suarez Morales
Joseph Rodriguez
Luis Bonilla Garcia
Casandra Luna
Adriana Tanajara
Dalia Martinez
Eunice Cordero Nazario
Fatima Arias Vilchez
Trey Jones
Aung Thain
Kyaw Khee
Manuel Gutierrez Bayin
Lineworker
Turkey Recipes & Tips!
Sorry, no recipe this week.
If you have any turkey recipes or tips you’d like to share please send them over and we’ll include them in an upcoming update!